The revolutionary potential of SLS 3D printing
SLS 3D printing has revolutionized the manufacturing industry by making it possible to create complex parts from powder. This process, also known as selective laser sintering, uses a laser to fuse powder particles, creating a solid part. This technology offers great design freedom and can produce high-quality parts with excellent mechanical properties.
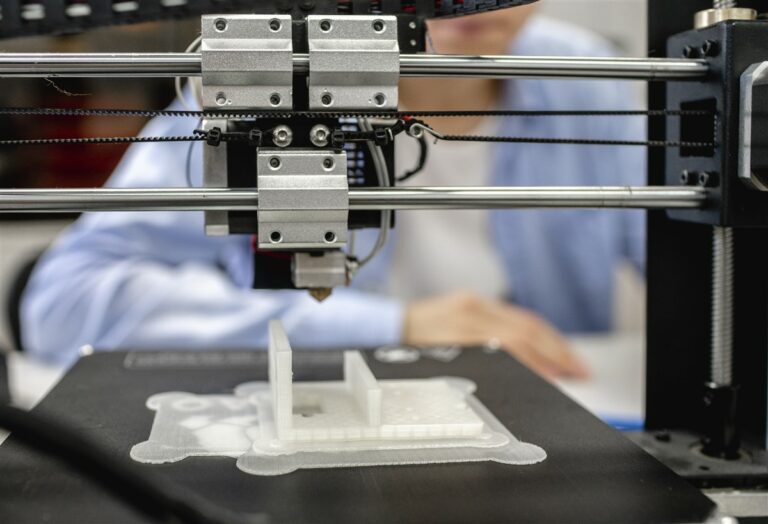
SLS printing is particularly suitable for the production of functional prototypes and small series of parts. It is capable of working with a wide variety of materials, including nylon, which makes it very versatile. As a result, you will find this technology used in fields as varied as aerospace, automotive, medical, or fashion.
Comparison with other 3D printing methods
Despite the growing popularity of SLS 3D printing, other 3D printing techniques, such as SLA printing and FDM printing, are also widely used.
SLA printing, or stereolithography, uses a laser to cure a liquid resin and create a part. While this method produces parts with excellent surface finish, it is less suitable for producing functional parts due to the brittleness of the materials used.
On the other hand, FDM printing, or fused deposition modeling, uses a strand of material that is melted and deposited layer by layer to build a part. This technique is relatively affordable and easy to use, but it is not capable of producing parts with the same complexity or precision as SLS printing.
The Challenges of SLS 3D Printing and How to Overcome Them
SLS 3D printing is not without its challenges. Despite its many benefits, it also has some drawbacks that can be addressed with an informed approach.
Post-processing of parts is one of the biggest challenges. After printing, parts must be cleaned of excess powder and often undergo post-processing to improve the surface finish. This can be a time-consuming and expensive process, but advances are constantly being made to simplify and make it more affordable.
Additionally, SLS printers are typically more expensive than FDM or SLA printers. However, the cost per printed part can often be lower with SLS printing, especially for small runs and prototypes.
Finally, intellectual property can be a major issue in 3D printing. Ensuring the protection of designs and ideas is crucial, but can be a challenge in an environment where digital files can be easily shared and copied.
Conclusion: SLS 3D printing, is the solution for your complex projects
SLS 3D printing is an additive manufacturing technology that has the potential to transform manufacturing by enabling greater design freedom and high-quality output. Despite some challenges, an informed approach and a good understanding of this technology can open new horizons for your projects.
Whether you are in the aerospace, automotive, fashion, or medical industries, SLS printing can help you produce complex and functional parts, while offering you unmatched flexibility and economy of scale. There is no doubt that SLS 3D printing is an innovative solution to solve your most complex challenges.